This event will highlight the latest commercially impactful developments and innovations in the field of renewable or green materials and food across a range of material classes and application areas. The event will feature world-class speakers from OEMS, promising start-ups, as well as renowned research centres, covering the development of renewable, green, and/or compostable materials derived from plant based sources or from novel techniques such as enzymes or other synthetic technologies. The material classes covered include all manners of plastics as well as functional materials applied in electronic and display industries. This event will be part of the TechBlick online event series and will be specifically co-located with an event on "Machine Learning in Material Development: Innovations, Start-Ups, Applications"

Avantium
Bineke Posthumus
Director Business Development

PEF, the next generation plant-based plastic with unique properties
Bio-based materials are desperately needed to replace fossil-based materials in the world’s transition to a sustainable packaging industry. The focus of this presentation will be on the polyester PEF (polyethylene furanoate). PEF is a plant-based, highly recyclable plastic, with superior performance properties, good mechanical performance and a greener production process compared to today’s widely used petroleum-based packaging materials.
The presentation will give the audience a better understanding of the polyester PEF, its value proposition in applications and the fit of PEF in the circular economy to reduce, recycle and regenerate.

CE Delft
Pelle Sinke
Researcher / consultant

LCA of cultivated meat production in 2030
Environmental research and consultancy organization CE Delft conducted a prospective Life Cycle Assessment (LCA) study of cultivated meat (CM, also sometimes referred to as cell-based meat, clean meat, cultured meat and in-vitro meat) to provide insight into the environmental impact of this product when produced at commercial scales in 2030. In it, CM is compared to conventional meats (beef, pork, chicken) and plant-based alternatives. This is the first LCA study which uses primary data from multiple CM companies and from associated companies in the CM supply chain, cross-checked by independent experts.
It can be concluded that CM can offer environmental gains compared to conventional meats, but has on average higher impacts than fully plant-based options. CM uses much less land compared to all conventional meats (due to more efficient conversion of feed into meat) and has less nitrogen emissions, both of which lead to reduced biodiversity impacts. It does have higher energy use than conventional meat production. Nonetheless, it has a much lower carbon footprint than beef and is comparable to current global average footprints for pork and chicken when produced using conventional energy. When using sustainable energy, CM has a lower carbon footprint than ambitious production benchmarks for all conventional meats.

Carbonauten
Anestis Dietrich Becker
Product & industrial design

Making materials and food sustainable and cheap
carbonauten is the minus CO2 factory and has developed a unique system for industry that reduces CO2 emissions and costs. This makes materials and food cheap.
The carbonauten system involves the production of a category of materials that is innovative in many respects: carbonauten NET-Materials® (Negative Emission Technology). They consist of a combination of biocarbons with various binders. As fillers and functional materials, their properties are improved compared to conventional materials.
The biocarbons are produced from biogenic and industrial residues by pyrolytic carbonization. Each ton of biocarbon stores up to 3.3 tons of CO2.
Other products include base-load renewable energy (heat, electricity, hydrogen) for further processing or processes in the industry, and high-quality distillates from pyrolysis oils as a platform for environmentally friendly biochemical products.
The material and energetic cascade use of biomass residues enables the production of large quantities, high qualities and low prices. This lowers economic hurdles and enables rapid transformation for the construction industry, builders, developers, and cities and communities.
Scaling is ensured through global, decentralized and technologically identical locations.
carbonauten will replace large quantities of fossil-based building materials, plastics, chemicals and fuels with at least 100 sites worldwide by 2030.

Econic-Technologies
Michael Kember
Co-Founder

Using Waste Carbon Dioxide To Make Valuable Polyurethane Products More Sustainable
In a world where CO2 emissions are ever increasing and creating havoc, it is imperative that individuals and companies alike adopt solutions that are kinder to our environment. For heavy emission industries, like construction and chemicals, carbon capture and storage is an option to offset emissions, but these technologies are typically expensive, do not generate value and cannot be implemented everywhere. Carbon capture and utilization, however, is significantly more attractive, especially when transforming CO2 adds value to existing industry. Econic’s ready-now technology enables polyol producers to do just this.
Econic’s innovative catalyst technology allows captured waste CO2 to be used as a raw material in polyols, replacing up to 50% of traditional oil-based feedstocks, in a low-energy, low-cost process. These CO2 containing polyols can be used in a range of everyday products, like mattresses, building and refrigerator insulation, cleaning products, sportswear and in cars.
Also possible, and specific here, is the introduction of waste CO2 into polyurethane products and surfactants, with Econic’s technology offering three pillars of added value to the product and the industry:
1. Economic: CO2 is an order of magnitude cheaper, and less volatile in price, than traditional oil-based feedstocks. Furthermore, Econic’s technology operates at low pressures and temperatures, so can be retrofitted onto existing manufacture assets, and means it has low-cost entry to market.
2. Environmental: As demonstrated in our recent LCA, for every tonne of CO2 that is used as a raw material in manufacture, a further three tonnes minimum of CO2 emissions are avoided. In the polyurethane and surfactants industries, this would be the equivalent of planting 19 million trees every year.
3. Performance: The unique tunability of CO2 content in polyols offers the ability for polyurethane and surfactants producers and end users to select the properties of the polyol to match the specific downstream applications.
In contrast to many ‘green’ chemical technologies, Econic’s technology combines improved economic, technical, and environmental performance in one sustainable package.

Fibenol
Uku Erik Tropp
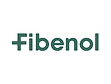
Hardwood processing residues to biomaterials and biochemicals: from dream to real in 5 years by example of Fibenol
Lignocellulosic biomass has been considered as abundantly available biobased feedstock to drive transformation of the industry towards more sustainable raw materials use. Despite focused efforts to scale novel conversion processes, then success has been limited. Fibenol is to bring the change, as unique pre-treatment technology was chosen to fractionate woody biomass at industrial scale, which allows extraction of high quality cellulosic sugars, near native lignin and specialty cellulose – sustainable raw materials to replace fossil based chemicals like bitumen, phenol, polyols, to use it as filler or functional additive in (bio-)plastics, use sugars as non- food competing raw material for fermentation processes etc. Fibenol is real, not anymore a dream and we have our sustainable raw material samples already available at ton scale to be tested out in diverse list of end use applications to set the scene for industrial production and supply within first half of 2023.

Fiberight
Dhivya Puri
Head of R&D




Fiberight – The End of Waste
Fiberight has developed an innovative resource recovery platform which captures recyclable materials from household and commercial waste. These waste materials are then upgraded into market-ready products to be used in the manufacture of new goods. The process is robust and works with mixed, contaminated waste inputs which are typically burnt or buried (landfill and incineration). The process can recover and recycle over 70% of the materials in residual waste, helping to increase recycling rates and reduce the associated environmental impact of waste disposal.
Fiberight is using demand-led innovation to develop and deploy high-value products from resources in waste. The output products include: paper and card pulp for pulp moulding applications; second generation sugars for biochemicals and biomaterials, purified plastic polymers for mechanical recycling and other traditional recyclable commodities.

ISARA
Jean-François Hocquette
Senior scientist

State of the art, update and gaps of knowledge about "cultured meat"
This talk has been prepared in collaboration with Marie-Pierre Ellies-Oury and Dr Sghaier Chriki.
The major challenges facing our evolving agri-food system nowadays are to provide enough food to the growing human population while protecting the planet, farm animals and consumer health. To meet these challenges, more and more FoodTech companies are proposing a disruptive technique based on laboratory food production: muscle cell culture to produce “meat”.
However, “cultured meat” is the subject of various controversies, including three major ones.
The first one concerns the ethical aspects not only about the potential to improve animal welfare, but also regarding the ethical values of our society with questions about food artificialisation, in a context where the demand for naturalness is high.
The second controversy concerns the environmental, health and nutritional aspects, i.e. the properties of "cultured meat" with an associated question: is it really meat?
The third controversy concerns its economic model, and above all how to produce it on a large scale? and at which cost? with which quality?
These three controversies interact with each other around technical, political, legal and societal issues. They concern the different visions of the World that citizens and stakeholders may have, including the total abolition of livestock farming for ideological reasons, or simply the reduction of intensive livestock farming, which is strongly criticised. Being in competition with other sustainable solutions for the future (reduction of food waste and loses, new habits of food consumption, development of agro-ecology, etc.) or simply with other meat substitutes (proteins from algae, plants, mycoproteins, insects), the future of "cultured meat" is questioned.

Jiva Materials
Jonathan Swanston
CEO

Soluboard: The World's First Fully Recyclable PCBs
Jiva Materials Ltd is a UK-based company that has developed and patented a fully recyclable printed circuit board (PCB) laminate - Soluboard.
Soluboard is constructed using natural fibres which have a much lower carbon footprint than the market incumbent glass fibres.
Soluboard also delaminates in hot water where precious metals from the electronic components are recycled and the organic fibres are repurposed.
This novel recycling process avoids the energy intensive incineration typically used for standard PCBs.
Soluboard is being trialled with multiple international customers interested in reducing the carbon footprint of their electronics portfolios.
Jiva is directly tackling the impact of electronic waste, the fastest growing waste stream in the world.

LanzaTech
Babette Pettersen
VP Europe

Capturing Carbon. Creating Value
LanzaTech converts carbon-rich gases into sustainable fuels and chemicals by a process of gas fermentation, with microbes that feed on gases rather than sugars, as in traditional fermentation. LanzaTech’s naturally-occurring microbe has been optimized to provide economic routes to ethanol, jet fuel and chemicals from a variety of carbon-rich gas streams, such as industrial off-gases from steel and ferroalloy mills, syngas generated from any solid resource, including agricultural waste, municipal solid waste (MSW), plastics waste and waste wood, and even CO2 from Direct Air Capture (DAC). By capturing the carbon contained in these gas streams, LanzaTech’s gas fermentation process reduces industry carbon emissions whilst producing sustainable aviation fuels and chemicals that serve as building blocks for a broad range of consumer products including household cleaning products and detergents, fine fragrances, packaging, textile fibers and fuels. Products made with LanzaTech’s process offer an improved environmental profile and reduce greenhouse gas emissions by over 70% when compared to equivalent products derived from fossil fuels.

Mango Materials
Allison Pieja
CTO

Transforming Biogas Methane into Biodegradable Polymers
Mango Materials is a Bay Area-based start-up that uses methane gas to produce biodegradable biopolymers that are economically and functionally competitive with conventional, oil-based plastics. Mango Materials produces powder or pellets of poly-hydroxyalkanoate (PHA), a valuable product that can be converted into a variety of high-margin or high-volume, environmentally friendly goods such as textiles, injection-molded packaging or other products, or films.
Methane is a potent greenhouse gas often produced as a byproduct at sites such as wastewater treatment plants, landfills, and agricultural facilities. In this process, biogas methane is directly utilized as a feedstock for bacteria, which produce PHA intracellularly in a fermentation process. The PHA is then separated from the non-polymer cell mass and used in a variety of downstream applications.
Mango Materials’ process is unique in that it utilizes methane and is thus focused on gas fermentation. The process is currently being scaled up, and Mango Materials operates its Launch facility at a local wastewater treatment plant (Redwood City, CA).

Mimotype
Claudio Flores
Founder & CEO
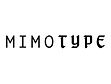
Bio-sourced and inspired organic light emitting (OLED) materials
OLED’s breakthrough moment requires new sustainable and purely organic materials. Our solution: Bio-inspired OLED. Molecules that emit light in living organisms are structurally closely related to those used in OLED. Evolutionarily optimized molecular structures promise highly desirable properties, i.e. stability, quantum efficiency and simplicity. Bio-inspired molecular designs offer key advantages compared to existing solutions: biocompatibility, -degradability and recyclability have already been proven by Nature. Our goal is to create an economy-of-scale for advanced bio-inspired OLED materials and devices firmly grounded on circular economy principles.

Mogale Meat
Paul Bartels
CEO

Cultivated Meat – A Potential Wildlife Game Changer
Fibroblasts, myoblasts and adipocytes are cultured from a small biopsies taken from a young animal. The cells are matured into muscle and fat cells and combined to form ground meat or whole-cut meat products. For the planet, and more specifically for southern Africa’s wildlife and biodiversity conservation, cultivated meat is a potential game changer. Additional natural habitat does not have to be ploughed-up for crop production to feed more factory-farm cattle needed to satisfy the increasing human populations demand for meat.
Cultivated meat R&D requires a multidisciplinary team approach involving professionals in veterinary science, bioengineering, bioprocessing, bio-medical, biotechnology and food science, animal production, environmental science and government agencies. Mogale Meat Co has cryopreserved over 700 cell cultures derived from game species as a resource for scientists from the Tshwane University of Technology and the University of Kwazulu Natal to develop the required technologies to make the production of cultivated meat a reality in southern Africa.

TBM
Eiji Mizuno
Assistant Division Head
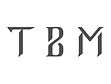
LIMEX an innovative material mainly made of limestone - A solution to reduce plastic with a stable price.
TBM is a company based in Japan specializing in developing, manufacturing, and distributing LIMEX, an innovative new material mainly made from limestone. It could be molded into plastic alternative products with existing technology and can be recycled. Flexible film packaging, food containers, and many other products could be made with this eco-friendly material. The basic patents of LIMEX have been registered in 40 countries and have been introduced to over 8,000 companies in Japan. LIMEX is registered in the sustainable technology dissemination platform "STePP" by UNIDO (United Nations Industrial Development Organization) as a recyclable material. By supplying LIMEX worldwide, TBM aims to solve plastic waste issues, resource depletion, and various environmental issues.

UBQ Materials
Derek Schaefer
VP Business Development

Invisible Plastics: The Opportunity for Climate Impact in our Supply Chains
Strategies to actualize net zero emission goals in the food industry cannot ignore the massive opportunity hidden within our supply chains. Nearly company utilizes extensive supply chains and logistics products that are packed with overlooked plastics - pallets, bins, crates, displays. Implementation of the right raw materials can transform our supply chains from liabilities into principal sustainability assets.
UBQ Materials converts unsorted household waste, including all organics, into a biobased thermoplastic. This novel material carries a powerful climate positive value proposition; for every ton of UBQ™ produced, nearly 12 tons of CO2eq are prevented. Seamlessly substituting oil-based resins, UBQ™ is able to reduce and even neutralize the carbon footprint of thousands of product applications without imposing additional costs.
Hear from UBQ Materials on how food and beverage giants such as McDonald’s, PepsiCo, ABinBev and Nestle are implementing their material and learn how a subtle production change can result in a big environmental impact.