We invite engineers, researchers, entrepreneurs, inventors, and end users from around the world to join TechBlick Innovations Festival on 25 April 2024 online
#AdditiveElectronics #PrintedElectronics #3DElectronics #WearableTextiles #TextileElectronics #SoftElectronics
#SustainableElectronics
This is a carefully curated event weaving together fantastic talks with superb networking and immersive virtual exhibition where you can move around with your own avatar.
The programme will cover all the key application and technology advancements, reflecting the beautiful diversity of this field.
The networking will happen in the immersive virtual platform as well as in round-robin speed networking sessions.
This event makes virtual interaction real and you will feel the buzz of meeting where you can have many spontaneous and serendipitous discussions.
Our last summer Innovations Festival 2023 had 700+ participants [not registrants]! Do not miss this opportunity!
BONUS: If you register now you will receive a discount code for attending our onsite Future of Electronics RESHAPED conference and exhibitions in Berlin and Boston!!

3E Smart Solutions
Steliyan Vasilev
Co-Founder & Development Engineer

Driving Reliability and Scalability in E-Textiles and Wearables via Embroidery Technology
Embroidery technology, once rooted in historic hand-stitched garment design, has experienced a remarkable resurgence with the advent of computerization. Due to its unparalleled capacity for material optimization, embroidery offers textile engineers the ability to precisely place single fibers,yarns, fiber bundles, or even wires in a pre-designed geometry. This precision makes embroidery an ideal candidate for integrating functionality into textiles through sensors, actuators, or electrodes. By enabling the automatic integration of conductive fibers and electronic components into textiles,embroidery technology facilitates the creation of e-textiles. This capability opens the door to a myriad of applications, ranging from ECG and EMS electrodes to capacitive, strain and pressure sensors, and even illumination systems and heating elements.Despite the longstanding development of e-textiles, the realization of market-ready products has been limited by high production costs and poor reproducibility resulting from manual production processes. The high degree of automations of embroidery technology, combined with the scalability enabled by multi-head machines, has revolutionized e-textile production. This automation not only reduces costs but also ensures consistent quality, paving the way for the widespread adoption of e-textiles in various industries.

ACI Materials
Len Allison




Breakthrough Conductivity and Sensing With
Semi-Sintered Silver Ink
In the dynamic landscape of New Product Development (NPD) at OEMs, engineers have long pursued the solution for fully additive processes (FAP) circuit board manufacturing. Traditional methods have been hampered by challenges such as subpar electrical performance of conductive inks, limited interconnect density, and the environmental instability of joints formed between isotropic conductive adhesives (ICAs) and surface mount devices (SMDs). These hurdles have confined FAP applications primarily to low-complexity devices, such as sensors and membrane touch switches. Enter ACI Materials and our groundbreaking Alchemy Conductive Inks. Our proprietary inks are set to transcend these longstanding barriers, heralding a new era of efficiency, sustainability, and versatility in the manufacture of Flexible Hybrid Electronics (FHE) compared to conventional PCB/FPC processes. Our presentation will explore the transformative features of Alchemy Conductive Inks that empower engineers and designers at OEMs to innovate with less constraints:

Akoneer
Tadas Kildusis
CCO
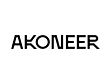
Going maskless for chip packaging with SSAIL
SSAIL technology enables direct writing of Cu on organic and other dielectric materials. This can be applied for RDL, fanouts and other features in heterogenous integration. High adhesion of the Cu layers increases reliability for demanding applications, like automotive or defense. With maskless process, single part batches and fast iterations are available.

Brewer Science
Adam Scotch



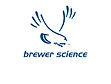
Towards Ubiquitous Water Quality Monitoring

CONDUCTIVE TECHNOLOGIES INC
Alicen Pittenger
Director of Sales
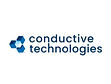
Innovation: A Contract Manufacturer's Perspective
Innovation doesn't just relate to the product itself; but the method in which it is manufactured. As your trusted contract manufacturing partner, CTI is always investigating new types of equipment, technologies, raw materials, etc to best suit the needs of our customers.

CondAlign
Salvatore Micali

Enabling Room Temperature Electronics Bonding In FHE Applications, Addressing Sustainability and Cost
Introduction
CondAlign is an innovative technology company that has patented and developed a new range of adhesive anisotropic conductive films (ACFs), to enable efficient components bonding for the flexible and hybrid electronics (FHE) industry. This new ACF named E-Align, provides excellent electrical and mechanical bonding performances, in particular to bond electronic components to flexible and rigid substrates.This ACF comes in the form of a double-sided tape, and it doesn’t require any post curing process. Its application process is also very simple, considering that doesn’t require any high pressure (typical bonding pressure is ca 0,1 – 0,3 MPa) or heat (it can be bonded at room temperature).Through these unique characteristics, the E-Align ACF has the ambition of simplifying the entire electronic production and assembly process, increasing efficiency and reducing costs.Presentation content In this presentation, CondAlign will start with an introduction of the technology principles behind the products development, will then provide an overview of the characteristics of the different ACF products already available in the market and the others under qualification, and will finally conclude with different examples of successful end user applications, where the E-Align ACF products enable sustainable and cost-efficient electronic bonding of different products for distinct industries. Examples of applications are the following: bonding printed batteries to printed IOT platforms for logistic and inventory tracking solutions, bonding flexible displays to flex-tails, bonding skin patches to wearable electronic medical devices, etc.

Danish Technological Institute
Zachary J. Davis

eTextile Sensors and More
This talk will provide an overview of Danish Technological Institute's capabilities within eTextile development. Dr. Davis will showcase prototypes within on-skin sensors and integrated heating elements. This presentation aims to give a comprehensive understanding of our advancements and innovations in the field of eTextiles.

E2IP Technologies
Fernando Zicarelli



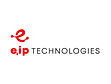
Screen-printing Heating Devices: Limits and Challenges
This presentation will review the most common screen-printed heaters in Printed Electronics; Printed Resistive heaters and Printed Wire heaters. An explanation will follow on how each type of heater is designed, and a comparison between a Printed Resistive heater (PTC) and a Printed Wire heater will be shared. There will be a review of the technology limits and challenges.Finally, a quick review of the latest technological advancements in Transparent heaters.

Holst Centre
Natallia E. Uzunbajakava

Advancing Medical Technology: Printed Electronics and Hybrid Integration Pave the Way for
Next-Generation Medical Devices
Chronic diseases became a silent epidemic and are responsible for about 70% of deaths worldwide. Efforts are imperative to shift this distressing trend and make strides towards better health outcomes. Wearable technology holds vast untapped potential across healthcare continuum – from hospital to home.Printed electronics and hybrid integration offers a versatile technological toolbox to create next generation medical devices. Realizing this, however, necessitates navigating several substantial challenges – from further developing printed electronics & hybrid integration modalities to addressing the right user needs. With collaborative efforts among a diverse ecosystem of companies, institutes, and healthcare organizations, each bringing their unique areas of expertise, we are optimistic about overcoming these challenges.

Hummink
Sahar Al Kamand
Sales Engineer

Pushing The Boundaries of Microbump Fabrication: The HPCaP Approach
High aspect ratio microbumps are vital in packaging applications, yet typical methods lack the control needed for dimension. HPCAP (High Precision Capillary Printing) Technology addresses this, offering high control over microbump fabrication & exceptional versatility in dimensions & materials. Based on Atomic Force Microscopy (AFM) , HPCAP simplifies complex microbump manufacturing into a single-step procedure. During this presentation, we will delve into the workings of HPCAP technology. Our aim is to provide a detailed exploration of how this groundbreaking technology facilitates the creation of microbumps. Furthermore, the presentation will underscore the vital role that HPCAP technology plays in both packaging and semiconductor repair applications.

INO-Žiri
Nives Vehar
INO Sales US
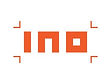
Demonstration of Flexible and Printed Electronics Production Using INO PE Line A7
Join us for a demonstration showcasing the production process of flexible and printed electronics utilizing the innovative capabilities of INO PE Line A7.Through screen printing in three colors, we will illustrate the smooth production of flexible electronic components with zero scrap, highlighting the efficiency and precision of this advanced production technology.Following the demonstration, attendees will have the opportunity to engage in a Q&A session to delve deeper into the intricacies of this innovative process. Don't miss this opportunity to witness the future of electronics manufacturing in action.

ImageXpert
Kyle Pucci
Director of Applications Engineering

Print Quality: All That Can go Wrong and How to Identify Them
In this presentation, we’ll dive into print quality for printed electronics and discuss techniques for analyzing it using machine vision. We will identify the most critical aspects of print quality, how to measure them, and what sort of equipment can be used to do this in a robust, repeatable way.

Intellivation LLC
Matthew Kleyn
Mechanical Engineer




Laser Patterned Sputter Coatings for Production of Two-Dimensional Multilayer Electronic Sensors
The demand for high-volume flexible devices across various industries necessitates advanced roll-to-roll (R2R) solutions utilizing vacuum coatings that are laser patterned. Various process and product controls are optimized to fulfill the specific requirements needed for different flexible devices. Modularity and scalability are critical for high volume production, these techniques can encompass these requirements along with ease of development.

KIMOTO
Menno Bos
General Manager

Adhesive Carrier and Protection Films for Advanced Manufacturing
Adhesives films play an important role during manufacturing processes, enabling scale-up and defect free production of printed electronics and display systems.
We will take a close look at available adhesive options and their suggested applications.

LinkZill
Dr. Linrun Feng
Founder & Co-CEO



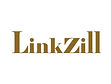
Innovating With TFT Technology in Both Optoelectronic and Biological Ways
LinkZill innovatively applies TFT semiconductor technology to various fields of optoelectronics and life sciences such as large-area bio-sensing, novel display, high-throughput DNA synthesis, and in-vitro diagnostics (IVD), based on our core TFT chip capabilities of in-situ signal sensing, pico-liter droplet manipulation, and microarray reaction control.

Linxens
Christelle Robellin
Healthcare Marketing Director

Scalable, Customizable, Multimodal Electrode Platform for Biosensors and Sensors
For over 15 years Linxens has manufactured hundreds of millions of PCB electrode arrays for Point-of-Care Diagnostics. This could be achieved thanks to a cutting-edge and robust reel-to-reel manufacturing process. Recent developments in electrode design, surface coating/functionalization, microfluidics and connectivity open up new fields of application in continuous monitoring of glucose, wound healing, water quality and sport performance etc.

Nagase ChemteX
Alan Brown
Business Development Manager

Conductive Ink Wash Testing
There are many challenges that Conductive Inks face when used in wearable applications. Of those challenges, washability is possibly the most challenging. In this presentation Alan Brown from Nagase ChemteX America Corporation (NCU) will discuss those challenges and recent developments in washability testing using conductive inks.

Neotech AMT
Martin Hedges




Additive Manufacturing of Sustainable Mechatronic Systems
This presentation will review the current status of the Additive Manufacture (AM) of sustainable mechatronic systems. The use of AM processes, offers significant sustainability advantages in the production of electronic and mechatronic systems by way of simplifying the materials mix, improved materials efficiency and heavily compressed process chains, localising manufacture. The fundamental technology combining free-form, 5 axis 3D printing of mechanical and electronic components, Surface Mount Device (SMD) placement and pre- and post-processing techniques, is described. The State-of-the-Art of the manufacturing process chain is demonstrated by way of a proof-of-concept of a lighting product

Niebling GmbH
Udo Weustenhagen
Director Sales & Marketing

High Pressure Forming (HPF) for In-Mold Electronics (IME) Processes
Precise 3D forming of substrates is the key to success when it comes to In-Mold Electronics. Not only the 3D forming need to be carried out precisely to fit perfectly into the injection tool cavity, but the positioning of the conductor tracks, the electronic components already positioned in 2D or even graphics must also be in the right position with repeat accuracy. The high-pressure forming process, which uses high-pressure air of up to 90 bar and significantly lower forming temperatures than traditional thermoforming, delivers all of these benefits. Clever automation modules can be used to automate the process for series production and link it to subsequent processes, such as trimming the film inserts after forming.

Printed Electronics Ltd
Neil Chilton

Scaling up From Idea to Product With The PEL Open-Access Printable Electronics Production Facility
For university spin-outs and startup companies, especially in the growing medical sector, it can be challenging to find a responsive production partner to scale up your idea from bench-scale to the small/mid volume production needed to gain investment and customers. PEL is an established manufacturing company with over 18 years’ experience in printable electronics. Here in the UK, we have an extremely well-equipped production facility that gives access to a multitude of printing methods including: high resolution screen printing, inkjet deposition, aerosol jet and viscous jet piezo jet deposition. Whilst some customers prefer to outsource their production entirely to us, we also engage with users who are keen to become manufacturers in the longer term – where they can be trained on the systems we sell and “try before they buy”. In this presentation we explain the capabilities and the training and support packages that PEL can offer.

Quantica
Ben Hartkopp
Founder, IP & Technology Manager

Why 3D printing has failed the electronics industry: A look into the failures & future of 3D inkjet for electronics applications
In this talk, Ben Hartkopp, one of the founders at Quantica, will address the fundamental issues at the root of the limited impact that 3D printing has caused in the electronics industry and reveals how upcoming changes in new 3D printing technologies technology are poised to address the industry's critical shortcomings. Despite the significant advancements in technology, the world of printed electronics still faces fundamental challenges and is missing key technological advancements that are essential for its progress. Hartkopp will provide an in-depth analysis of the current printed electronics landscape, highlighting the persistent gaps and limitations that hinder its full potential. Within this context, you will gain a deep understanding of the unique demands of electronics manufacturing and how traditional 3D printing methods have fallen short. These limitations have not only hindered innovation but also contributed to inefficiencies, waste, and economic challenges within the industry. Throughout the talk, you will discover how Quantica's groundbreaking additive manufacturing technology, NovoJet, aims to fill these critical gaps and revolutionize the industry. By focusing on PCB manufacturing as a starting point, Quantica's innovative drop on demand material jetting solution promises to reshape the electronics industry. By enabling the use of novel high viscosity and high particle loaded materials from leading industry partners for the design and generation of substrate and conductive geometries, Quantica's NovoJet represents a transformative leap forward. Learn how NovoJet addresses these technological shortcomings, setting the stage for a digital deposition revolution that promises positive societal, economic, environmental, and climate impacts without the negative consequences that have plagued the industry.

SmartKem
Simon Ogier
CTO

Organic Thin-Film Transistor Technology – from Lab to Fab
OTFT technology is finding a good fit initially in applications requiring low temperature processing and is suitable for situations where low non-recurring investment (NRE) or capital infrastructure is required. Smartkem OTFT materials are processed with a low thermal budget and produce transistors with current driving capabilities suitable for a range of emissive displays such as AMOLED and micro-LED. This presentation will highlight application demonstrators and show the partnerships that are enabling scale up of the fabrication towards commercial scale production.

TracXon
Corne Rentrop
Project Leader

Sustainable Mass-production of Hybrid Printed Electronics
The talk will focus on sustainable advances through implementing printed electronics. Thereto methods are explained to minimise energy consumption and reduce CO2 footprint. Next to that the talk discusses recycling strategies of printed electronics. To complement the talk methods are explained to manufacture complex products and allow a sustainable alternative for PCB

VTT
Jussi Hiltunen
Research Professor
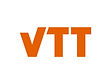
Wearable Photonic Sensors in Flexible and Stretchable Form Factor
Medical device industry is a rapidly growing opportunity area for photonics technologies, with applications ranging from diagnostics to surgical tools and therapeutics. Real-time monitoring of vital parameters with unobtrusive wearable devices can minimize the time of patients in hospital and ultimately the technologies can enable a paradigm change from treatment-based healthcare towards preventive and participatory medicine. For example, optical monitoring of hearth rate, blood pressure, physical activity and other parameters can minimize risk for post-treatment complications and subsequent treatment costs and enhance the quality of life. Besides healthcare, in wellness applications wearable devices help citizens to better track, for example, the stress levels and thus optimize the amount and level of exercises. A key issue in the production of wearable devices with the maximized user comfortability, is the manufacturing process capable for assembling and integrating devices in flexible and stretchable form factors. At high volumes this can be made using multiple roll-to-roll fabrication processes covering printing of electrical wiring and stop&go component assembly. As an outcome the wearable photonic monitoring devices can be highly sophisticated acquiring multimodal data or low-cost plaster-type devices intended for a short term usage.