Keiron | When InkJet Doesn't Work: Deposition Via Lift Technology
- khashayar Ghaffarzadeh
- Jul 11, 2022
- 5 min read
This article was written in a collaboration between Keiron Printing Technologies and LMNS by Roland Biemans and originally published in Specialist Printing Worldwide: Issue Two: 2022.

Contact: Marco van Hoorn
Email: info@keirontechnologies.com
Phone: +31 (0)40 209 7074
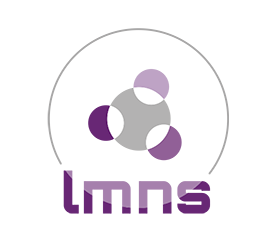
Laser-Induced Forward Transfer (LIFT) printing is a high precision, non-contact method of printing materials that cannot be deposited through existing print processes. Roland Biemans, Founder/Owner of LMNS, a group offering independent print industry expertise, delves into the technology and its uses.
The intelligent electronic skin
The printing industry is ever-expanding into new application fields. Besides long-accepted traditional processes, innovative technology paves the way toward digital and hybrid methods that allow going beyond promotional and decorative printing. In particular, where it concerns functional and industrial printing, the search for alternatives continues when screen, transfer or inkjet processes are unable to offer a solution. One such alternative is LIFT, or Laser-Induced Forward Transfer printing; a high precision, non-contact method to print materials that are too viscous, too expensive or simply too difficult to be deposited through existing print processes.
"LIFT is based on the principle of using laser pulses to jet material off of a donor plate for deposition onto a receiving substrate"
Inkjet is known for its versatility in various industries, notably promotional graphics and decorative printing of full-colour images, where ink formulations are tailored to mimic traditional processes, but with the characteristics to run through small printhead nozzles. Most are either dye-based or have a relatively low amount of small pigment particles as a colourant. The solid content is usually kept to a minimum to promote stability and runability. Formulations are typically based on a primary carrier such as water or oil, and additives to control the stability of the composition and process such asco-solvents, humectants, surfactants, resins and initiators. In all cases, inkjet inks are developed with the application in mind and must be compatible with the substrate they are printed upon, or with the primer or pre-treatment of the media to which the colourant will bind. It is a delicate balance between having a fluid that has the right rheology to be jetted without any issues, yet, at the same time, delivering the right wetting and drying characteristics and material quality so that once it is deposited onto the receiving surface, it will perform according to the required fastness properties.
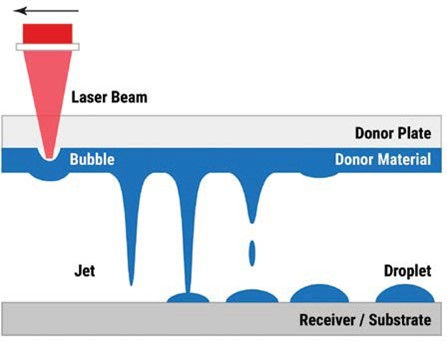
A donor plate holds the material that needs to be deposited onto the substrate. A laser pulse agitates the material to form a jet. Visit Keiron virtual booth
Deposition Challenges
One of the bigger challenges has been to formulate an ink that will allow the formation of droplets that have the right size, velocity, directionality and frequency when being jetted from the printhead without having solid particles eventually blocking nozzles. The emergence of recirculation printheads has greatly enhanced the bandwidth of inkjet performance and it certainly has decreased clogging issues. As such, inkjet research is increasingly directed at printing non-decorative industrial and functional fluids with higher solid particle loads or functional components such as silver, gold, copper or graphene. But what if the application requires a non-contact deposition method with ultra-high precision that surpasses inkjet capabilities? What if the particle size or solid content volume prevents proper jetting with a nozzle? And what if the cost per drop in relation to the volume of ink is so high that precision and accuracy are more important than productivity? Stacking or layering solid particles in a pattern with a positioning precision of less than five microns is not an easy feat. In an application field where, for instance, conductivity in thin lines is needed, both accuracy and precision need to be warranted to prevent circuit interruption. This deposition requirement for repeatability alone is one of the key factors in choosing a printing process. And inkjet is often not capable of successfully reaching this accuracy level; certainly not when it concerns jetting material with a viscosity of 300cP or higher, and a particle load of 50wt% or more.
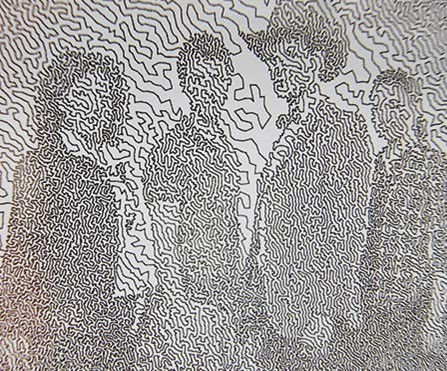
Figure 1: Close-up photo of a LIFT printed glass surface, using silver nanoparticle ink from PV Nano Cell. Line thickness is approx. 100 microns / 0.1mm. Visit Keiron virtual booth
A viable alternative could be LIFT printing, where the solid content and the viscosity is not limited by the restrictions of a printhead. Instead of trying to tailor a fluid to the relatively narrow bandwidth of inkjet, LIFT is based on the principle of using laser pulses to jet material off of a donor plate for the deposition onto a receiving substrate.
The Lift Print Process
The donor plate, usually a transparent carrier substrate such as glass, quartz or fused silica, is homogeneously coated with the deposition material. This is mostly done by spin-coating or blade-coating. The donor material can be solid, fluid or paste. The donor plate is positioned directly above the receiving substrate, which can be a flexible foil, a rigid media, or any other object such as a panel, a machine component or (semi-) finished product. A laser beam is focused on the donor layer and a pulse initiates a gas pocket that expands to form a jet. Depending on the type and combination of laser beam and optics, the dot diameter, pulse frequency and intensity are configured. Jetting speeds depend on the LIFT system set-up; the example used in this article (see Figure 1) is printed by Eindhoven-based Keiron Printing Technologies with a firing frequency of up to 300kHz with a single laser beam jetting a dot diameter of 100 microns.
"Stacking or layering solid particles in a pattern with a positioning precision of less than five microns is not an easy feat"
Where inkjet typically uses one and the same ink formulation in a system set-up and a preset print mode (single-pass/multi-pass, resolution/drop-size, dithering/screening, etc.), LIFT allows for the exchange of donor plates and variable donor materials in the same production run. Stacking or layering of different fluids and materials using the same deposition technology opens up possibilities for a hybrid printing approach.
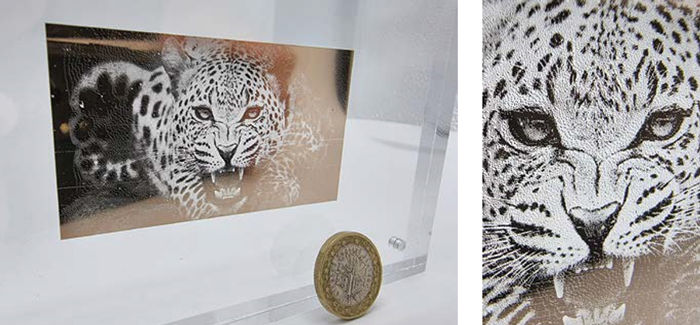
Complex patterns and structures can be printed at high speed and high precision. The quality of the deposition depends on the quality of the donor plate coating. Visit Keiron virtual booth
Application Fields
Although LIFT seems promising, it has been, to a large extent, a niche technology slow to gain traction with a wider audience. The technique is not new: in fact, in the late 1960s, the first patent describing the operating principle of LIFT was filed. In the 1980s LIFT as an acronym was coined and the process was tested as a novel technology to deposit metals and oxides.
"LIFT has seen successful application uses for the deposition of inorganic, organic and living material"
By now, LIFT has seen successful application uses for the deposition of inorganic, organic and living material. For medical and pharmaceutical application fields, bioprinting is an area of interest, with possibilities in cell tissue engineering and protein deposition. Moreover, printed electronics is an application field that LIFT has been tested on extensively. Think sensors, antennas and solar cells, for instance. Due to its non-contact, high-precision, high-speed jetting performance, LIFT is a promising printing technology that enables deposition of viscous and precious material.

Video still: LIFT uses laser pulses to jet material off of a donor plate and deposit in onto a receiving substrate. Visit Keiron virtual booth
At the ESMA IPI conference taking place 18–19 May 2022 in Düsseldorf, Keiron will showcase its technology platform and the various application fields it has been researching. As part of the HighTechXL deep tech venture building programme in Brainport Eindhoven, with partners such as TNO Holst Centre, Keiron started off with the intention to create a platform for the production of ‘lab on a chip’ devices. More recently, the start-up company has secured funding allowing it to build its first alpha tool.
Innovations Festival: Printed, Hybrid, 3D, InMold, Textile Electronics
24 June 2022 | 13:00 - 19:00 CET | Virtual Event Platform
Keiron will be having a virtual booth at the Innovation Festival. Visit Keiron virtual booth
Comments